Local & Overseas Manufacturing Solutions.
We have the unique ability to utilise local, modernised manufacturing facilities in all aspects of producing commercial equipment, which is particularly useful for short run, time sensitive products.
With a wealth of experience in manufacturing shopfitting equipment, having been in the industry for many years we’ve established local and offshore facilities that can accommodate any volume and price point required by their clients.
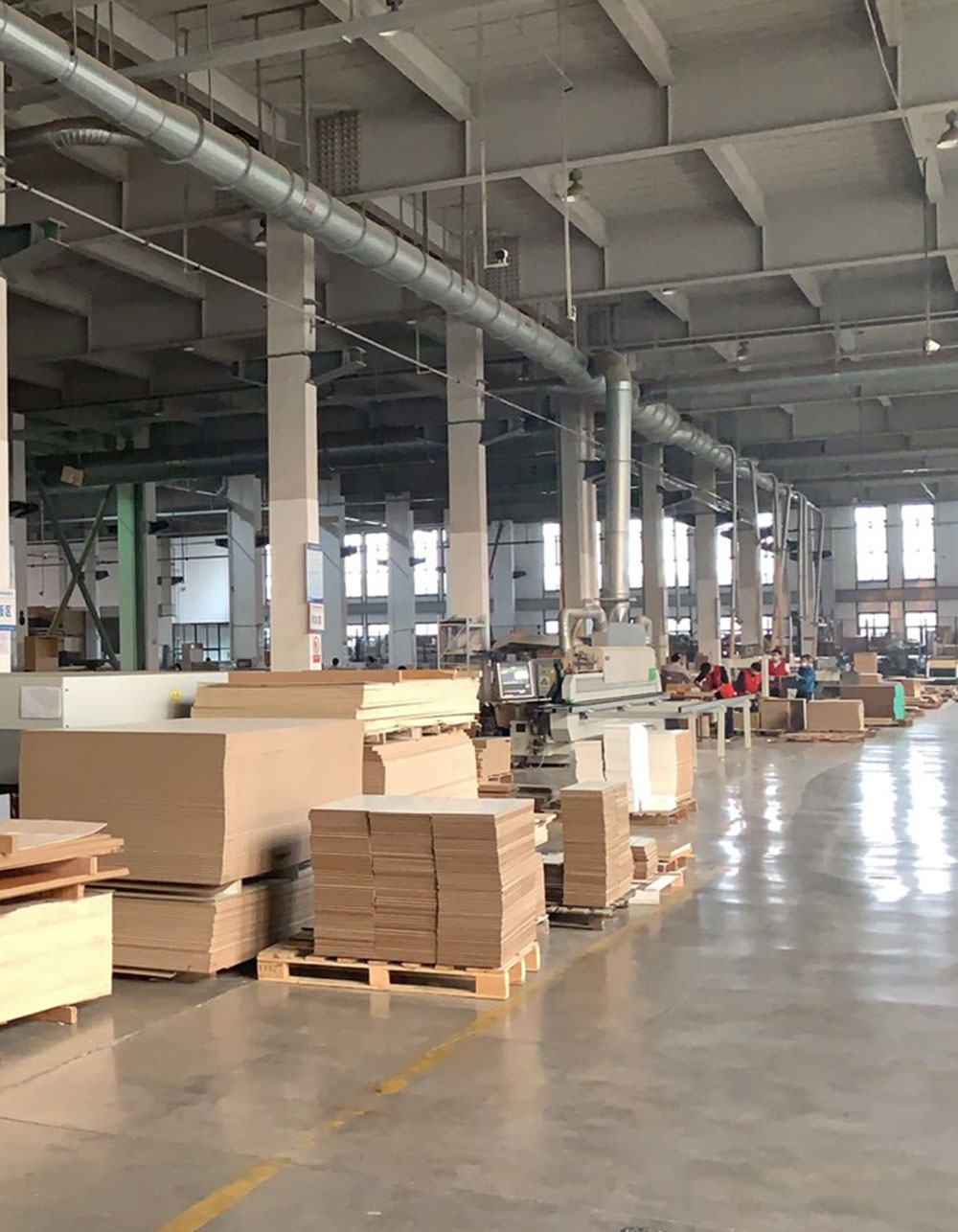
We Find a Way!
Our manufacturing capabilities enable them to offer customized solutions that meet the specific needs and requirements of their clients. They have a team of experienced designers and engineers who can work closely with clients to develop solutions that are tailored to their unique needs. This includes everything from custom signage and displays to specialized storage and shelving solutions.
In addition to their customization capabilities, Roar Equipment also has a range of standard products that are designed to meet the needs of a variety of retail environments. These products are manufactured to the highest quality standards and are designed to be both functional and visually appealing.
Roar Equipment's experience in manufacturing shopfitting equipment, combined with their customization capabilities and range of standard products, makes them a trusted and reliable supplier in the retail industry. They can work closely with clients to develop solutions that meet their unique needs and provide ongoing support and maintenance to ensure the long-term success of their shopfitting projects.
Beyond our local services, we have partnerships with overseas facilities that can provide almost any product (from either their catalogue, or our own design) in bulk supply and short runs. With our own staff on the ground in these areas, we can provide.
- Administration
- Cost-efficient pricing
- Sourcing
- Translation
- Quality control checks (prior to any product being packaged and loaded into containers for dispatch)
The general lead time for new a product is 4-6 weeks from the time of order. We have partners in metal, wire, joinery, plastics, electronics, glass, and many more.
Partners in China
Roar Equipment has established strong relationships with manufacturers in Asia and has expanded by opening a trading company in China. Having dedicated staff in Roar China shows our commitment to advancing in various manufacturing areas and sourcing a wide range of products.
Roar China
With offices in Shanghai and Foshan, Roar China has strategically positioned itself in two important industrial hubs in China. Shanghai is known for its international trade and finance, while Foshan is renowned for its manufacturing capabilities, especially in sectors such as metalwork, joinery, acrylic, electrical control engineering, and LED lighting.
By having local offices in these cities, Roar Equipment can benefit from the expertise and resources available in these regions, enabling smoother communication, efficient operations, and better understanding of the local market dynamics. It also demonstrates your commitment to maintaining a strong presence in China, a country known for its manufacturing prowess.
With Roar China's ability to source a wide range of products and the partnerships they have established; Roar Equipment is well-positioned to cater to diverse customer needs. This expansion and dedication to fostering relationships with manufacturers in Asia highlight Roar Equipment's commitment to growth and ensuring a reliable supply chain for our customers.
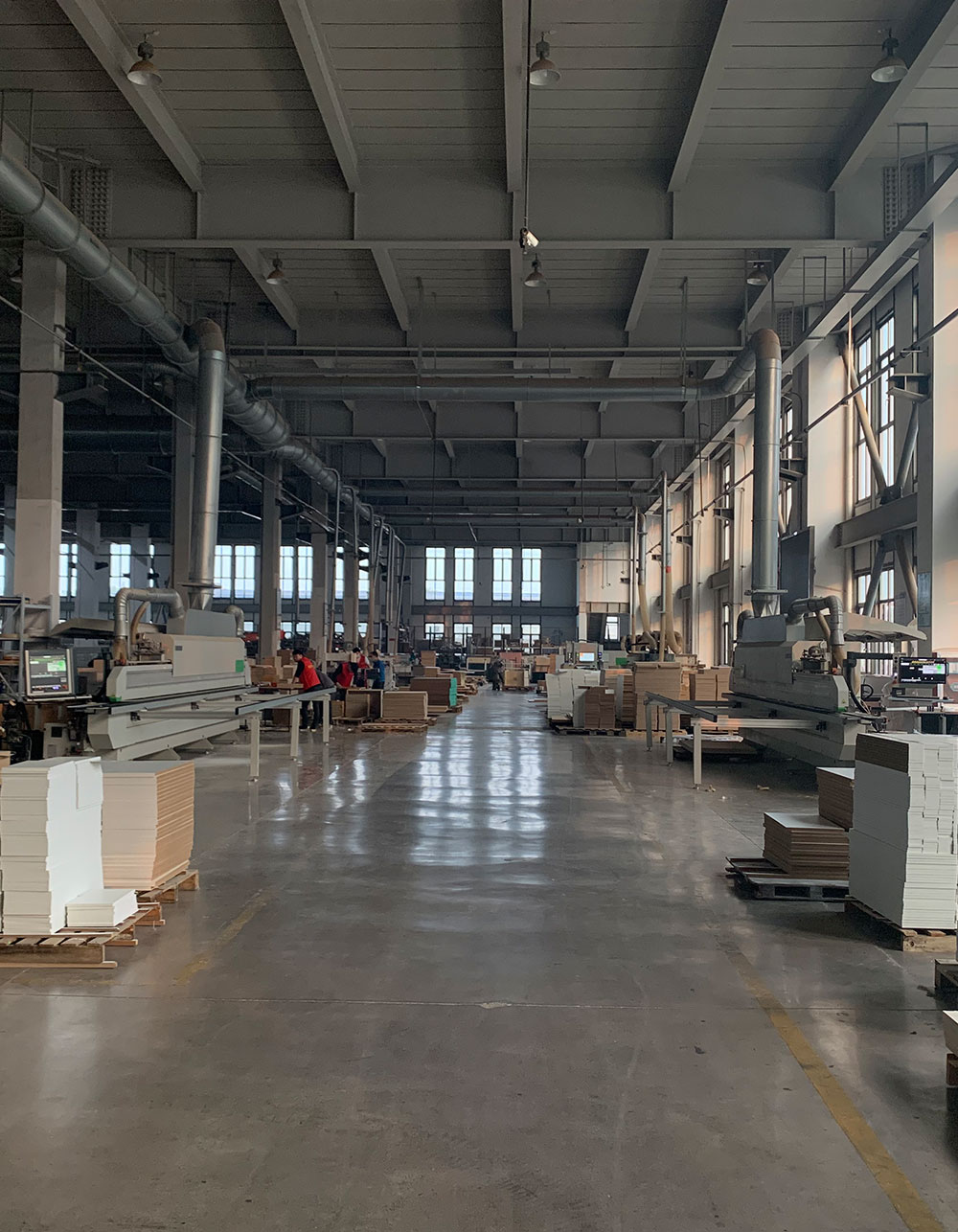

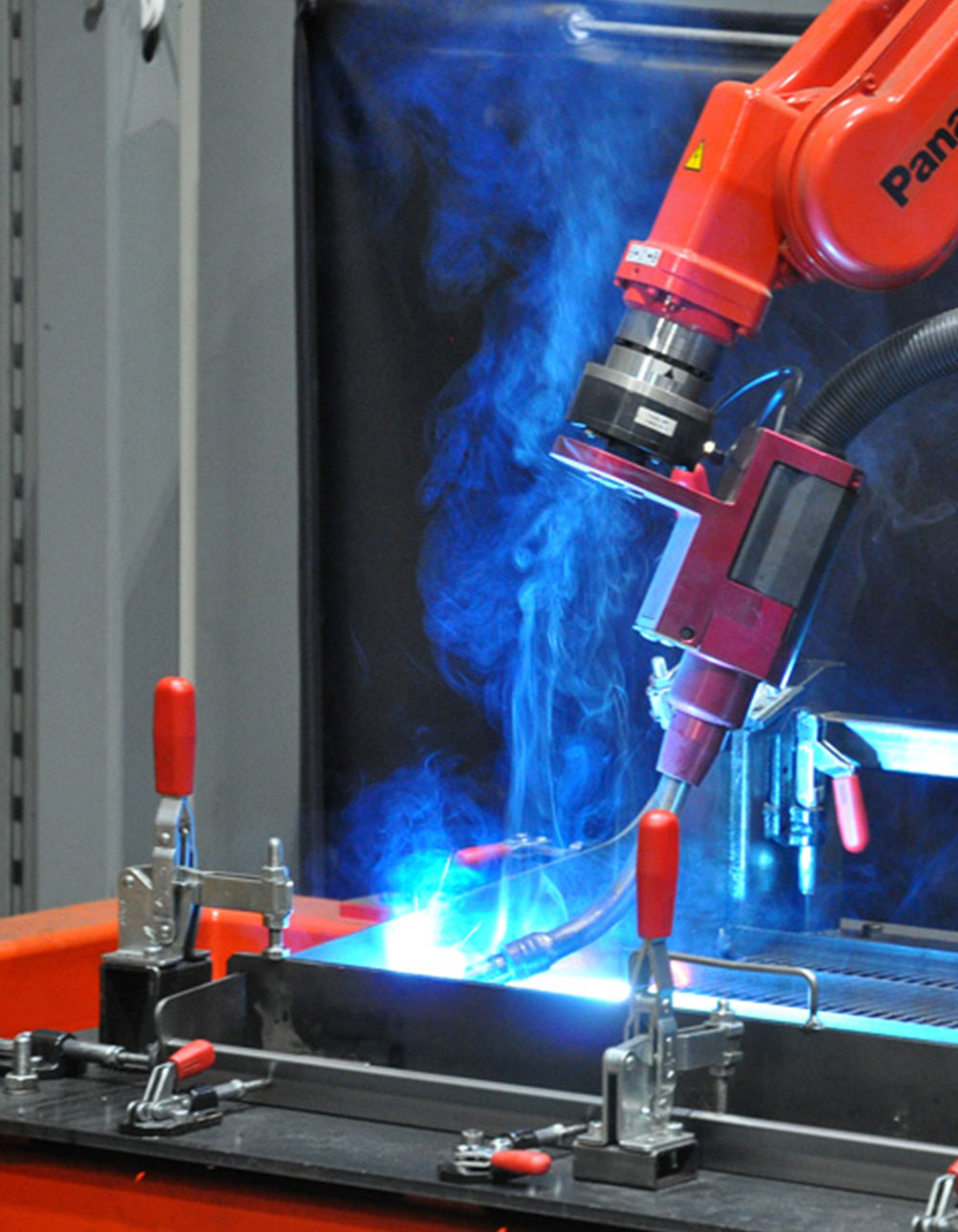
Partners in Europe
Metal Production
Metal processing production line covers a wide range of manufacturing processes in metal processing:
- Sheet metal cutting is carried out on an automatic line for lengthwise and crosswise cutting, which is by its size adapted to the needs of further production, whether it’s about creating profiles for storage systems or items for shop equipment.
- Cutting of items is carried out on CNC machines and a laser cutter. This technology represents the top quality of metal processing which enables the production of various profiles including maximum production flexibility as far as size and quality of offers are concerned.
- Wire products are manufactured on CNC machine.
- Metal sheets are bent on a variety of machines adapted to cover all demands of the market – from single items to batch production.
Lines for continuous profile bending represent our core technology and are used for:
- Creating profiles for all storage systems in our production. Profiles are continuously rolled on these lines, being cut to the required length per customer’s request.
- Making shelves and backs of store equipment systems, which retains flexibility of item size next to a very fast production.
- Sheet metal bending on benders in the case of small batch production offering a great flexibility in item measures.
- Bending on CNC bending machine.
Manual and robotic welding of welding positions:
- welding robots are used to produce positions via warehouse software, i.e. all positions produced in large batches. This technology ensures the production of equal positions of high quality
- manual welding is carried out by qualified welders with long-term experience in the production of warehouse and shop equipment
Finishing off position is carried out in our production plant by electrostatic powder coating or galvanizing. Both processes are performed on the new lines, meeting the required high standards of finishing process and taking environmental issues into account at the same time.
Powder coating of positions is carried out on two lines that provide a very high production capacity. The procedure of powder coating includes chemical cleaning and preparation of positions for robot painting and baking in flow-furnaces. The paint is applied in special paint booths which allow changes of colour within 10 minutes, providing quite a wide range of colours of our products.
Warming up the lines is done by hot air which is heated by a system connected to the biomass stove. Thermal oil is the stove’s agent, which is a new technology specifically developed for our needs. This system supplies all our processes with energy – from the powder coating line, galvanizing plants to central heating of our production lines and office premises.
Biomass heating system has given us energy self-sufficiency and ensured even greater care for the environment.
Partners in Europe
Wood Production
Production plant for the processing of solid wood and wood products is one complete unit which allows maximum adjustment to customers’ needs and desires, and consists of:
- Cutting out of chipboard panels, MDF, plywood and other panel products, which is carried out on an automatic cutting machine programmed to optimize workpieces
- Edge banding machine enables the application of multi-coloured strips – from thin melamine tapes, ABS tapes, to thin solid slats. ABS edges are also banded on a curvilinear edge banding machine
- Panel workpieces can be enriched by a veneer in a wide range of textures according to customer’s request
- Related to the processing of solid timber we can choose between two drying options within our own facility, i.e. a rapid drying in a vacuum dryer with automated process control or a gradual drying in the air to stabilize the material before further processing
- We process solid timber in our own facility using machines that allow semi-automated complete machining to a desired shape (multi-blade saw, planer thicknesser, solid wood panels gluing press, four-sided milling machine, sander)
- The final shape of products and semi-finished products is made on CNC machining centers
- Automatic machining center for window and door production rounds off the offer within wood processing procedure. External woodwork is manufactured from finished multi-layered euro-profiles of selected local or exotic materials, with the possibility of producing wood/aluminum system, which extends its durability and stands for the maximum quality regarding its usage. Windows are equipped with top quality seals, and optionally also with a special glass offering better thermal and sound insulation.
- Final painting of positions is done in a water curtain paint booth in a wide range of colours and various types of surface protection made of water or polyurethane varnish, high-quality translucent and opaque coatings, etc.
- Modern shapes and structures of warm wood elements per customer’s request can be complemented with glass, mirrors and acrylic glass, which is cut, bended and sandered in our own production plant
- Production process is rounded off in the assembly and packaging department, equipped with an appropriate technological equipment suited for a flexible working regime
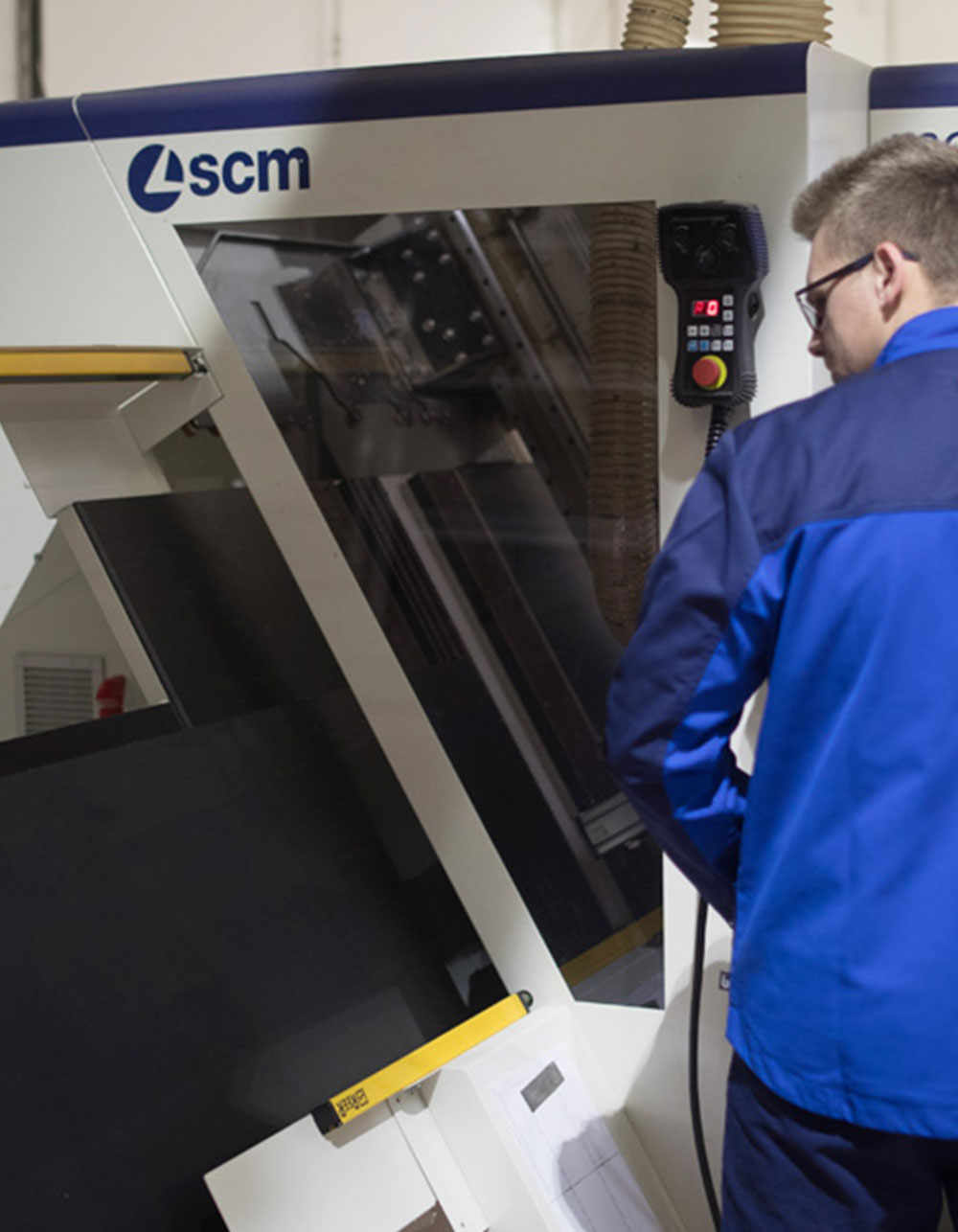
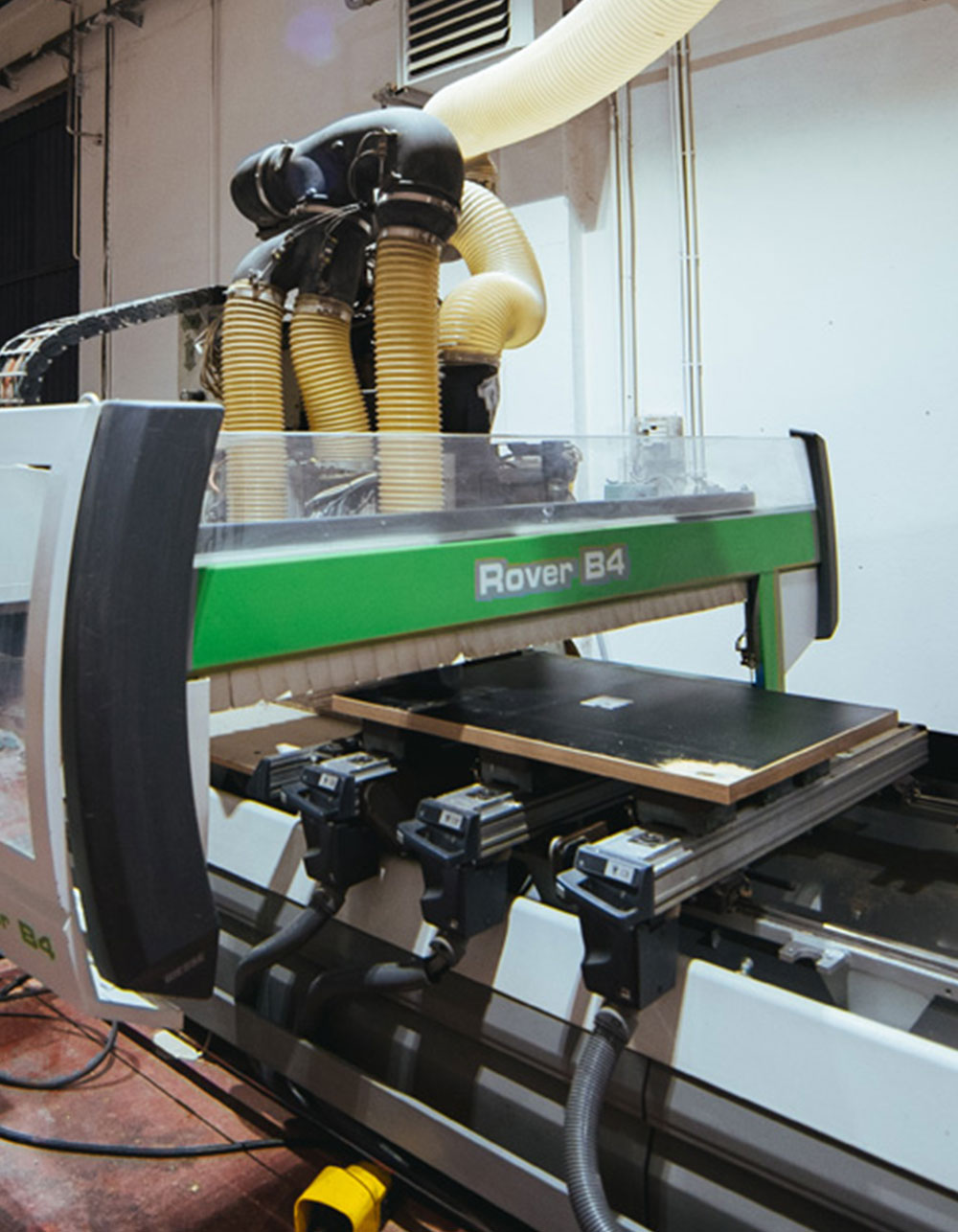
Testimonials
Work better with Roar Equipment today.
To many, shopfitting is simply fitting out a retail space with fixtures and fittings, but we look at shopfitting on a much larger scale.
Through the identification of key areas, we have been able to provide our clients with a far greater service than just ‘fitting out a retail space’. This is where evolution meets innovation.